Badania jakości wyrobów elektronicznych. Badania niezawodności urządzeń półprzewodnikowych
Wraz z rozwojem technologii elektronicznej liczba zastosowań elementów elektronicznych w sprzęcie stopniowo rośnie, a niezawodność elementów elektronicznych stawiane są coraz wyższe wymagania.Podzespoły elektroniczne są podstawą sprzętu elektronicznego i podstawowymi zasobami zapewniającymi wysoką niezawodność sprzętu elektronicznego, którego niezawodność bezpośrednio wpływa na pełną sprawność roboczą sprzętu.Aby pomóc Ci w dogłębnym zrozumieniu, poniższa treść jest dostępna w celach informacyjnych.
Definicja kontroli niezawodności:
Badanie niezawodności to seria kontroli i testów mających na celu wybranie produktów o określonych cechach lub wyeliminowanie wczesnych awarii produktów.
Sprawdzanie niezawodności Cel:
Po pierwsze: wybierz produkty spełniające wymagania.
Po drugie: wyeliminuj wczesną awarię produktów.
Znaczenie kontroli wiarygodności:
Poziom niezawodności partii komponentów można poprawić poprzez odfiltrowanie produktów, które uległy wczesnym uszkodzeniom.W normalnych warunkach wskaźnik awaryjności można zmniejszyć o połowę do jednego rzędu wielkości, a nawet o dwa rzędy wielkości.
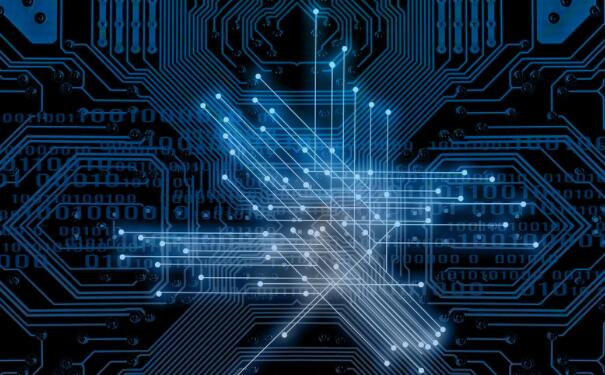
Funkcje sprawdzania niezawodności:
(1) Jest to badanie nieniszczące dla wyrobów bez wad, ale o dobrych parametrach użytkowych, natomiast dla wyrobów z potencjalnymi wadami powinno spowodować ich uszkodzenie.
(2) Sprawdzanie wiarygodności to 100% test, a nie kontrola wyrywkowa.Po badaniach przesiewowych nie należy dodawać do partii nowych trybów i mechanizmów awarii.
(3) Sprawdzanie niezawodności nie może poprawić wewnętrznej niezawodności produktów.Ale może poprawić niezawodność partii.
(4) Sprawdzanie wiarygodności zazwyczaj składa się z wielu elementów testu niezawodności.
Klasyfikacja kontroli niezawodności:
Kontrolę niezawodności można podzielić na rutynową i specjalną kontrolę środowiska.
Produkty stosowane w ogólnych warunkach środowiskowych muszą zostać poddane jedynie rutynowej kontroli, natomiast produkty stosowane w specjalnych warunkach środowiskowych muszą oprócz rutynowej kontroli przejść specjalne badania środowiskowe.
Wybór rzeczywistego przesiewania zależy głównie od trybu awarii i mechanizmu produktu, według różnych stopni jakości, w połączeniu z wymaganiami niezawodności lub rzeczywistymi warunkami pracy i strukturą procesu.
Rutynowe przesiewanie klasyfikuje się według właściwości przesiewania:
① Badanie i badanie przesiewowe: badanie mikroskopowe i badanie przesiewowe;Nieniszczące badania przesiewowe w podczerwieni;PIND.Nieniszczące badania rentgenowskie.
② Kontrola uszczelnienia: kontrola wycieków poprzez zanurzenie w cieczy;Badania przesiewowe w zakresie wykrywania nieszczelności przy użyciu spektrometrii mas z helem;Badanie wycieków znaczników radioaktywnych;Badanie przesiewowe w zakresie wilgotności.
(3) Badanie naprężeń środowiskowych: badanie wibracji, uderzeń, przyspieszeń odśrodkowych;Badanie szoku temperaturowego.
(4) Kontrola życia: kontrola przechowywania w wysokiej temperaturze;Badanie starzenia mocy.
Przesiewanie w specjalnych warunkach użytkowania – przesiewanie wtórne
Przegląd komponentów dzieli się na „przesiew pierwotny” i „przesiew wtórny”.
Przegląd prowadzony przez producenta komponentów zgodnie ze specyfikacjami produktu (specyfikacje ogólne, specyfikacje szczegółowe) komponentów przed dostawą do użytkownika nazywany jest „przesiewem wstępnym”.
Ponowna kontrola przeprowadzona przez użytkownika komponentu zgodnie z wymaganiami użytkowania po zakupie nazywana jest „przesiewem wtórnym”.
Celem wtórnego przeglądu jest wybranie komponentów spełniających wymagania użytkownika poprzez kontrolę lub test.
(przesiew wtórny) zakres stosowania
Producent części nie przeprowadza „jednorazowej kontroli” lub użytkownik nie posiada szczegółowej wiedzy na temat elementów i naprężeń związanych z „jednorazową kontrolą”
Producent części przeprowadził „jednorazową kontrolę”, ale element lub stres związany z „jednorazową kontrolą” nie może spełnić wymagań jakościowych użytkownika dla części;
W specyfikacji komponentów nie ma szczegółowych zapisów, a producent komponentów nie ma specjalnych pozycji do sprawdzania z warunkami sprawdzania
Elementy wymagające sprawdzenia, czy producent komponentów przeprowadził „jedno badanie” zgodnie z wymogami umowy lub specyfikacji, lub czy zasadność „jednego przeglądu” wykonawcy budzi wątpliwości
Przesiewanie w specjalnych warunkach użytkowania – przesiewanie wtórne
Elementy badania „wtórnego badania przesiewowego” można odnieść do elementów badania głównego badania przesiewowego i odpowiednio je dostosować.
Zasady ustalania kolejności elementów kontroli wtórnej to:
(1) Na pierwszym miejscu należy wymienić tanie pozycje testowe.Ponieważ może to zmniejszyć liczbę kosztownych urządzeń testujących, a tym samym obniżyć koszty.
(2) Elementy przesiewowe rozmieszczone w pierwszym powinny sprzyjać ukazaniu się wad elementów elementów w drugim.
(3) Należy dokładnie rozważyć, który z dwóch testów, szczelności i końcowego testu elektrycznego, jest pierwszy, a który drugi.Po przejściu testu elektrycznego urządzenie może ulec awarii z powodu uszkodzeń elektrostatycznych i innych przyczyn po teście szczelności.Jeżeli środki ochrony elektrostatycznej podczas próby szczelności są odpowiednie, próbę szczelności należy z reguły umieścić na końcu.